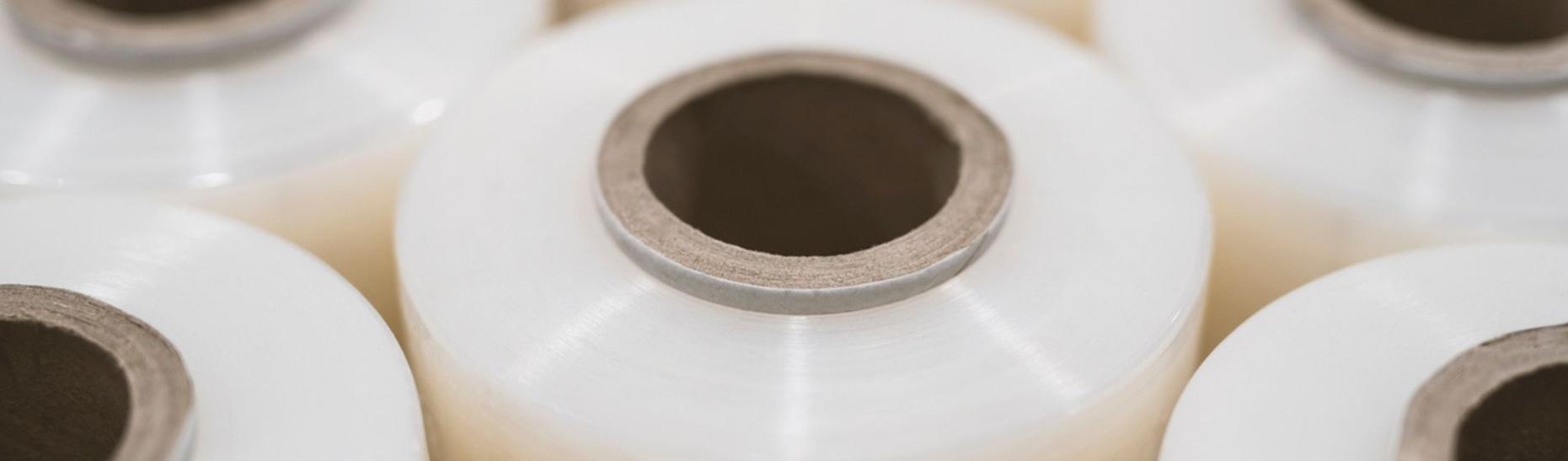
Below are five ways to cut your film consumption by getting the most from your stretch wrapping machinery without impacting on your load containment requirements.
Regularly viewing your wrapping methods and thinking strategically is critical in maximising efficiency. Are your current methods achieving optimal speed or slowing your processes down? Investing in stretch wrapping machinery and pairing it with the correct film is an excellent way to improve warehouse productivity and significantly reduce total long term costs.
1. Use the right film
Ensure the film’s properties suit the goods being transported and are appropriate for the machine’s stretching capabilities. Optimising the stretch film to match the load and machinery provides the best chance for the load to arrive in good condition.
A simple way to reduce film usage is to use high performance stretch films. Advances in film resins and extrusion technology means high performance films can be manufactured with lower gauges, thereby minimising direct cost and maximising metreage, while offering at least similar, if not enhanced, characteristics and functionality of heavier gauge films.
Alternatively, when compared to blown films, conventional cast films usually provide a lower cost per wrapped pallet, and improve the clarity allowing barcodes to be easily scanned through the film. Cast stretch film can be identified by the high clarity & low unwinding noise.
2. Know your machine
There is a wide range of stretch film machines available, with a variety of mechanisms used to stretch the film prior to applying it to the pallet. The different mechanisms have varying abilities to stretch the film so it is important to match the stretch capacity of the film with the machine's stretch capability.
Friction brake machines are a lower cost option designed to stretch the film by applying resistance directly on the film roll. The amount of applied stretch is adjusted manually via a handle/brake system.
Electromagnetic brake magnet machine provides enhanced stretch through a clutch system that applies force to the main roller creating a small amount of stretch. The force applied can be adjusted on the main control panel.
Power pre-stretch machines apply a nominated percentage of stretch to all films via the gearing of the machine. These gears set the rollers at two different speeds causing the film to stretch as it passes through. This is the most effective stretching mechanism as it allows the film to be stretched further to improve load retention and reduce wrapping costs.
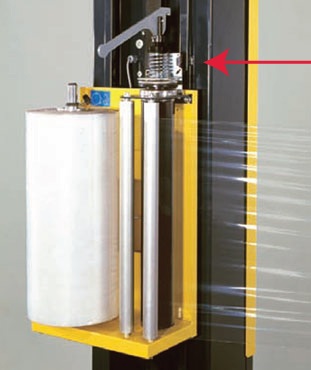
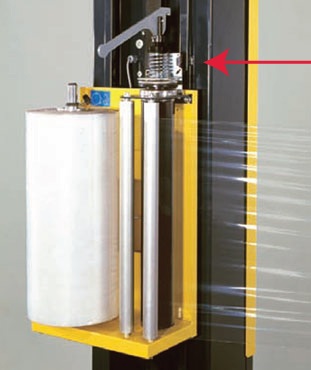
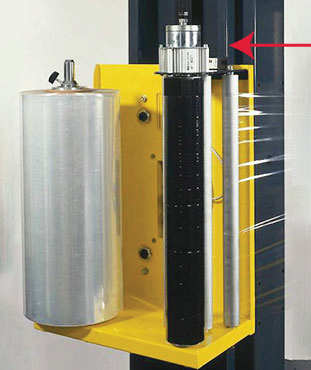
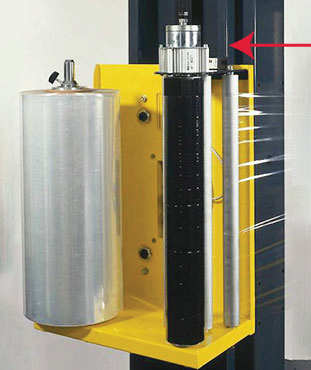
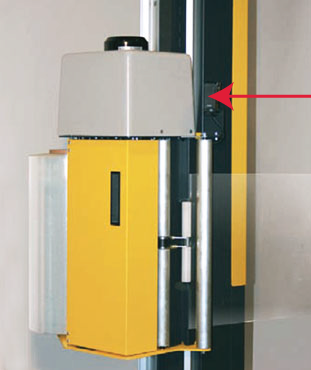
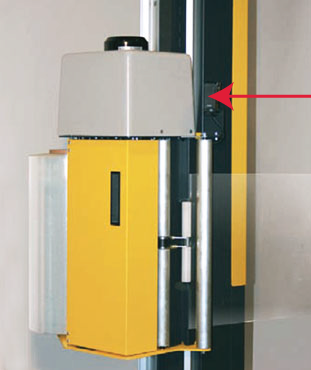
3. Check your overlap
The perfect amount of overlap is a significant contributor to load containment, while too much overlap will increase film waste. Ensure that the overlap of the stretch film during the wrapping cycle is adequate by adjusting the carriage and/or turntable speed.
4. Train your team
To further ensure your loads are secure, wrapping processes are efficient and loads are not being over-wrapped, staff members who regularly use the machines should be trained in the full operation of the wrapper.Signet recommends having a standard operating procedure (SOP) for all stretch wrapping machines, and Signet can facilitate Load Containment Workshops to help team members understand the importance of correct wrapping procedures.
5. Maintain your machine
Machinery maintenance is one of the critical aspects of ensuring that film costs are minimised and load containment is optimal. Some of the signs associated with poor maintenance are dirty or misaligned rollers, reduced stretching capabilities, turntable malfunctions and machinery breakdowns. All of these problems can increase costs, slow production, impact load containment or result in changing to heavier gauge, more expensive films. Preventative maintenance programs will enable the machinery to continue to perform efficiently and provide consistency in your pallet wrapping practises.